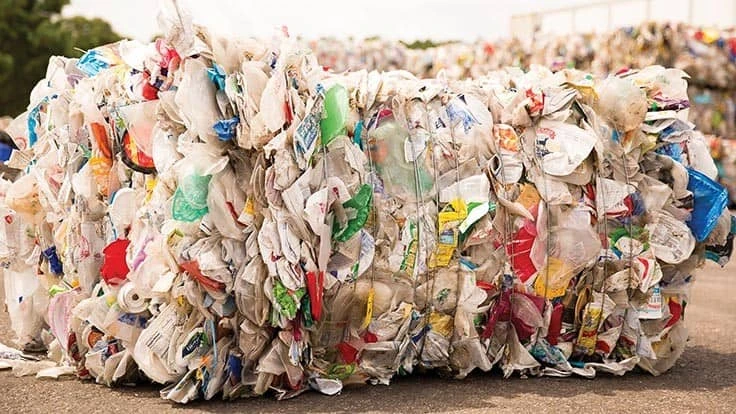

Polypropylene (PP) is an important packaging material that is sometimes overlooked and undervalued in the United States’ residential recycling stream. But that trend is rapidly changing, as the value of recycled PP has increased nearly tenfold over the past year. Material recovery facilities (MRFs) and PP reclaimers across the country are investing to capture sort and process postconsumer rigid PP packaging, returning that material to the manufacturing supply chain for use in new products and transforming PP from an undervalued material to a recognized and valuable commodity.
Traditionally captured in MRFs as part of Nos. 3-7 plastics and mixed plastics bales, PP appears in various formats, such as yogurt cups, margarine tubs, cold cups, food-service containers and coffee pods. The variety of packaging formats can make capturing PP more challenging than some traditional packaging types, such as high-density polyethylene (HDPE) milk jugs or polyethylene terephthalate (PET) bottles, but it also further proves the value and versatility of the material in packaging and preserving everyday products.
By analyzing robust datasets from capture studies performed at the curb, The Recycling Partnership, which is headquartered in Falls Church, Virginia, estimates an average of 17 pounds of PP can be found per household per year in the U.S. This estimate put residential PP volumes on par with those of natural or colored HDPE and would make the material the third-most prominent plastic in the recycling bin, behind PET and HDPE.
WHY PP IS OVERLOOKED

While PET and HDPE have been recognized in the recycling stream for decades, PP is the new kid on the block. MRFs that traditionally handle large volumes of materials, particularly fiber, plastic bottles and metal cans, quickly are recognizing the need to upgrade their facilities to capture other significant materials in the stream, such as PP.
According to the most recent recycling access report from the Sustainable Packaging Coalition, Charlottesville, Virginia, for the How2Recycle label, 59 percent of U.S. households have access to PP recycling, meaning residents can put PP containers into their recycling bins for sorting at the MRF.
How2Recycle is a standardized labeling system that communicates recycling instructions to the public. However, in light of the impacts from China’s National Sword Policy, some MRFs around the country are struggling to find end markets for their traditional Nos. 3-7 bales in which PP is sometimes captured.
Because of uncertainty around how many of those programs ultimately could be landfilling or incinerating the material postcollection, How2Recycle gave PP its “Check Locally” label in early 2020.
Through June, seven material recovery facilities have received grants to upgrade their equipment through the Polypropylene Recycling Coalition.
INCREASING PP RECOVERY
To address the challenges facing PP recycling, The Recycling Partnership brought together stakeholders including brands, retailers, manufacturers, resin converters, reclaimers, nongovernmental organizations and industry associations in July of last year to form the Polypropylene Recycling Coalition. The coalition’s founding steering committee members are Keurig Dr Pepper, Braskem and the Walmart Foundation.
The Polypropylene Recycling Coalition set out to catalyze rapid change in PP recycling by providing grants to MRFs to install equipment in their facilities to better sort and capture PP. By sorting specifically for PP, these facilities can increase the end-market viability of the PP in their stream by selling PP-only bales, commonly known as “Tubs and Lids.” The result of these upgrades is not only an increase in recycling access for the households served by these MRFs but also an increase in the supply of postconsumer recycled PP—a material brands and manufacturers are eager to purchase for use in their products.
Within six months of launching its grant program, the coalition received more than 50 applications from MRFs interested in making facility upgrades to sort and capture PP. The coalition has provided seven grants to MRFs as of late June and plans to announce several more grantees by the end of summer. Overall, the coalition aims to provide more than a dozen grants within its first year.
The coalition also has achieved its goal of increasing PP recycling access by more than 5 percent in the first year. This means millions more U.S. residents will have access to PP recycling, contributing more than 6,000 tons per year of additional postconsumer recycled PP for use in new products.
This growing momentum behind PP recycling and building recycled PP supply is supported by rapidly increasing demand for recycled PP. More than 500 companies signed on to the Ellen MacArthur Foundation’s New Plastics Economy Global Commitments to increase the recyclability and recycled content of their products by 2025.
Meanwhile, the U.S. Plastics Pact, launched as part of the Ellen MacArthur Foundation’s global Plastics Pact network and led by The Recycling Partnership and World Wildlife Fund, announced its Roadmap to 2025 earlier this summer, which is a national strategy for achieving 2025 targets specifically in the U.S.
The coalition’s work is done in close alignment with the U.S. Plastics Pact Roadmap to define and address the PP-specific challenges and appropriate targets for PP resin and formats. In short, sustainability commitments have been made, a road map has been outlined, and the coalition is serving as the key action agent to drive PP recyclability and recycled content forward over the next five years. Stakeholders across the PP value chain are stepping up to support these actions as companies work toward achieving 2025 goals for plastic recycling.

Investments for the future
Achieving these commitments will be no small feat. A recent report by The Recycling Partnership, “Paying it forward: How investment in recycling pays dividends,” cites a $17 billion funding gap in the infrastructure and consumer education needed to fix the U.S. residential recycling system and truly build a more circular economy for packaging. In the absence of policy, filling this funding gap will require private investment from stakeholders across the packaging value chain to begin to address the most significant issues in the system.
Organizations have already stepped up to meet this need, with private investments by facilities and operators themselves; grant funding from nonprofits, foundations and government agencies; and even low-interest loans from venture capital and financial institutions.
The coalition leverages a combination of grant funding and private facility investments to activate rapid change, with recipients making equipment installations within six months, on average, of receiving grant funding. In just one year, the coalition provided nearly $5 million in grants and catalyzed an additional $10 million in private investments to inject much-needed capital in PP sorting within MRFs across the country.
The amount of grant funding varies by MRF, depending on the needs and opportunities of each project, ranging from a few hundred thousand dollars to multiple millions of dollars. It also depends on the MRF as some MRFs plan to upgrade one piece of equipment, while others will perform retrofits or new builds with the funding.’
Uses of the funding include (but are not limited to) optical sorting equipment; robotic sorting equipment; conveyor systems; bunker or other storage systems for sorted material; processing equipment that results in PP acceptance or improved PP processing; and dock space or related investments to facilitate PP shipping. Grantees provide details on the overall investment, including sources of funding, such as private funds, loans or other grant funds, as well as information on the best equipment upgrade for their unique operations.
The MRFs that have received funding as of June are:
- American Recycling in Candler, North Carolina;
- Cougles Recycling in Hamburg, Pennsylvania;
- Dem-Con Cos. in Shakopee, Minnesota;
- Independent Texas Recyclers in Houston;
- Mazza Recycling in Tinton Falls, New Jersey;
- Rumpke Recycling in Cincinnati; and
- Winters Bros. in Brookhaven, New York.
This ready capital, along with the data and best management practices around education supplied by The Recycling Partnership, is enabling these MRFs to identify PP opportunities within their facilities and take swift action to invest, capture and begin marketing this increasingly valuable commodity.
Sponsored Content
Lawn and Landscape Marketing on a Budget
Digital marketing can feel overwhelming when you’re working with a limited budget. Websites, SEO, social media, and paid ads can quickly add up, but you don’t need to do everything to see results. By focusing on cost-effective strategies, you can still make a big impact without overspending.
Sponsored Content
Lawn and Landscape Marketing on a Budget
Digital marketing can feel overwhelming when you’re working with a limited budget. Websites, SEO, social media, and paid ads can quickly add up, but you don’t need to do everything to see results. By focusing on cost-effective strategies, you can still make a big impact without overspending.
Sponsored Content
Lawn and Landscape Marketing on a Budget
Digital marketing can feel overwhelming when you’re working with a limited budget. Websites, SEO, social media, and paid ads can quickly add up, but you don’t need to do everything to see results. By focusing on cost-effective strategies, you can still make a big impact without overspending.
Sponsored Content
Lawn and Landscape Marketing on a Budget
Digital marketing can feel overwhelming when you’re working with a limited budget. Websites, SEO, social media, and paid ads can quickly add up, but you don’t need to do everything to see results. By focusing on cost-effective strategies, you can still make a big impact without overspending.
Sponsored Content
Lawn and Landscape Marketing on a Budget
Digital marketing can feel overwhelming when you’re working with a limited budget. Websites, SEO, social media, and paid ads can quickly add up, but you don’t need to do everything to see results. By focusing on cost-effective strategies, you can still make a big impact without overspending.
Sponsored Content
Lawn and Landscape Marketing on a Budget
Digital marketing can feel overwhelming when you’re working with a limited budget. Websites, SEO, social media, and paid ads can quickly add up, but you don’t need to do everything to see results. By focusing on cost-effective strategies, you can still make a big impact without overspending.
The grant recipients each demonstrated a commitment to marketing PP and were able to show end-market access and an understanding of the markets available to them for PP. The current grant recipients are all in the early stages of equipment installation and implementation. All of these MRFs are expanding their capabilities to accept and specifically sort PP; many of them have recognized high volumes of PP in their stream and are looking to optimize capture.
For PP, speed is of the essence. With companies tracking toward 2025 recyclability and recycled-content goals, materials and packaging types already are being assessed on their ability to achieve circularity. Fortunately, PP is well on its way with the rapid investment and changing landscape catalyzed by the Polypropylene Recycling Coalition.
The precompetitive collaboration demonstrated through the The Polypropylene Recycling Coalition has proven to be a successful model to facilitate rapid change and will be applied to address gaps in circularity for other materials and packaging formats. Action-based grants drive the speed of change needed and help lead to sustainable scaling when followed by low-interest loans and, ultimately, policy. Together, these activities will provide future funding that the U.S. residential recycling system needs, giving it a chance to evolve into a true circular economy—and PP has a clear role in that future.
Get curated news on YOUR industry.
Enter your email to receive our newsletters.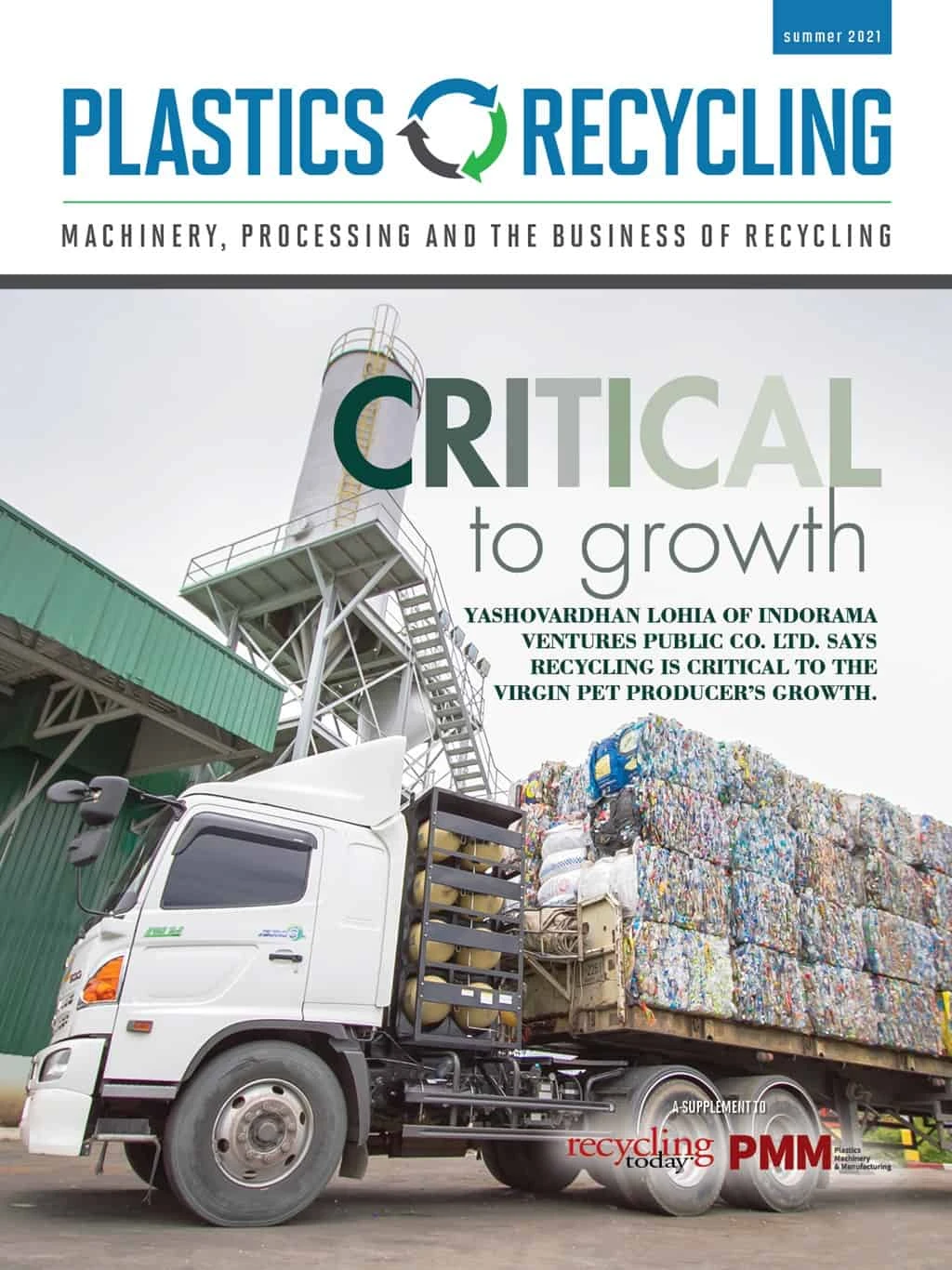
Explore the Summer 2021 Plastics Recycling Issue
Check out more from this issue and find your next story to read.
Latest from Recycling Today
- ReMA board to consider changes to residential dual-, single-stream MRF specifications
- Trump’s ‘liberation day’ results in retaliatory tariffs
- Commentary: Waste, CPG industries must lean into data to make sustainable packaging a reality
- DPI acquires Concept Plastics Co.
- Stadler develops second Republic Services Polymer Center
- Japanese scrap can feed its EAF sector, study finds
- IRG cancels plans for Pennsylvania PRF
- WIH Resource Group celebrates 20th anniversary